Резервы улучшения результатов работы склада. Мероприятия по повышению эффективности работы склада
За последние 10-15 лет представление о современном складе изменились кардинально. Современный идеальный склад – это склад, которого нет. В современном представлении товар, пылящийся на полках в ожидании очередного заказа – это если не преступление, то дорогостоящая некомпетентность. Современные логистические сервисы стремятся сократить время между датой производства и датой потребления. И хотя повышение надежности процессов и связанный с этим подход JIT (точно-во-время), влияют на существенное снижение запасов, все же склады и промежуточные запасы необходимы. Мы уже рассматривали как рассчитать оптимальный уровень запасов в . Итак, если запасов не избежать, что может быть предпринято?
Как же сократить потери и снизить расходы на складские операции? Давайте рассмотрим некоторые идеи бережливого производства, которые могут быть полезны в оптимизации запасов, сокращении затрат и увеличении прибыли. Все идеи могут быть разделены на три основные группы:
- Техническая и технологическая инфраструктура склада (погрузочно-разгрузочные комплексы, системы хранения грузов, полы, техника для перевозки грузов, расположение мест хранения и т.д).
- Организация работы или эффективность операционных действий (скорость обработки информации и принятия решений сотрудниками склада, количество действий и операций необходимых для получения груза со склада и т.д)
- Системы контроля и координации действий, необходимые для прослеживания и идентификации грузов (координация действий между работой погрузчиков и операторов склада)
Оставим рассуждения по поводу технической оснащенности складов более профильным специалистам, а поговорим о возможных подходах в отношении улучшения операционной эффективности.
Идея 1: Сокращайте объемы хранения запасов.
Как уже было сказано лучший способ хранения – это исключить необходимость хранения. Выработка операционной стратегии в отношении запасов, может существенно изменить количество и структуру запасов. Знание уровней минимального и максимального хранения, а также точек дозаказа даст четкую картину о наличии лишних запасов и поможет смоделировать необходимые площади для хранения.
Идея 2: Сокращение количества складских операций
Чем больше времени затрачивается на обработку одной единицы товара, тем дороже она обходится. Учитывая тот факт, что таких единиц на складе очень много, есть смысл задуматься о способах сокращения расходов в этой области. Первым шагом стоит сделать устранение дублированных функций. Стоит внимательно исследовать все операции, выполняемые сотрудниками. Опыт показывает, что большая часть из них - это выполнение никому не нужных требований (заполнение журналов, оформление документации по требованию бухгалтерии, о которых последние часто даже не подозревают и т.д.). Поступление и приемка товара - это один из тех процессов, которые должны быть выполнены одноразово. А система, по которой один человек получает материалы и согласно списку отправляет их на размещение, а потом отдает этот список на обновление данных, малоэффективная и устаревшая. Поэтому необходимо использовать как можно более точные способы для получения и размещения материалов. Есть несколько простых правил:
- База данных инвентаря должна обновляться, как только товар поступает на склад.
- Чем больше раз производятся эти операции и чем больше людей в них задействовано, тем больше времени и денег тратится впустую.
- Избавьтесь от способа подтверждения получения товаров с помощью ручки и бумаги.
- Используйте штрих-код материала для уточнения его количества и отправки в место хранения.
- Используйте хорошее программное обеспечение, в котором все базы данных обновятся одновременно, что облегчит получение информации вовремя и избавит от дублированных операций.
Идея 3: Передача операций на ранние этапы.
Существенно можно повысить эффективность логистических операций, если их часть передать на предыдущие этапы. Например, если товар переправляется со склада на склад, то упаковка уже может иметь универсальную маркировку, которая применяется на обоих складах, что исключит необходимость пересчитывать и маркировать упаковку. Или например, материалы, которые поступают на склад, помечаются RFID-метками до того, как они покидают производство с целью облегчить будущие процессы.
Идея 4: Идентификация и отслеживание товаров.
Следующим шагом по оптимизации склада должно стать использование надлежащей системы управления информацией. Работники бережливого склада точно знают, где хранятся материалы, и не тратят часы на поиски той или иной единицы.
Первым шагом к созданию бережливого склада является система стандартизации пространства, где хранятся грузы. Система 5С на складе – простой, не дорогой, но очень эффективный метод сократить потери, связанные с поиском груза, утратой информации, пересчету товаров и так далее.
Следующий не менее эффективный метод – это современные технологические способы идентификации. Например, штрих-коды и радиочастотная идентификация товара (RFID) . Они помогают добиться отличных результатов при правильном использовании. Первые имеют невысокую стоимость, вторые, пусть и стоят дороже, являются многоразовыми и имеют множество других преимуществ. Они могут хранить большой объем информации, а также получать информацию с больших расстояний. Необязательно находиться близко к запасам и считывать информацию с каждой RFID-метки. Радиометки - это ценный операционный интеллект, с помощью которого можно как оптимизировать маршруты погрузки и транспортировки, так и отслеживать запасы, срок хранения которых истекает.
Идея 5: Оптимизация расположения стеллажей:
Кроме того, важно уметь использовать складские площади. Возможно, в одной части помещения, полки переполнены, в то время как в другой они пусты. Если вы постоянно работаете над расширением площади склада – нужно задуматься над инвестированием в оптимизацию использования имеющегося места.В этом могут помочь, современные системы многоуровневого хранения. Немаловажную роль сыграют и расстановка стеллажей. К примеру исследования показывают, что расстановка Flying V . помогает сэкономить до 15% лишних транспортировок.
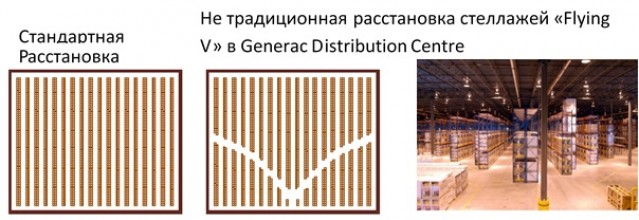
Идея 6: Использование алгоритмов сбора товаров.
Это технологии
компанийуровня Amazon
, оптимизирующие принятие решения о минимальной траектории движения, необходимого для сбора грузов для отправки. На рисунке продемонстрирован принцип использования алгоритма оптимизации движения. Эффективный склад должен быть спроектирован и организован таким образом, чтобы он соответствовал потребностям вашего предприятия. Это важно для того чтобы избежатьпотерь на перемещение по складу. Необходимо задуматься, сколько поездок делают работники, собирая заказ для отправки, и как организовать помещение так, чтобы сократить количество перемещений.
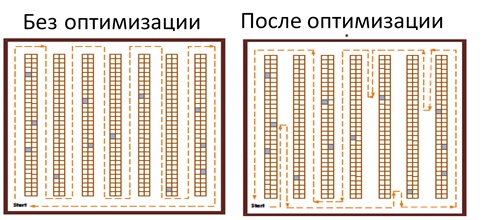
Больше об этих алгоритмах можно узнать от специалистов более узкого профиля. Например , “Routing order pickers in a warehouse with a middle aisle,” European Journal of Operational Research, vol. 133, no. 1, pp. 32–43, 2001..
Идея 7: Оптимизируйте места хранения товаров.
Наиболее распространенным методом анализа трудозатрат является "A ВС анализ" товаров, которые хранятся на складе. ABC – классификация товаров означает, что в зоне наиболее близкой к зоне отгрузки находятся товары с наиболее высокой частотой заказов. Зона «В» - это средняя частота заказов и так далее вплоть до неликвидов. Такой анализ можно проводить несколькими способами. Наиболее простой – использование статистики заказов для ранжирование товаров. В тех случаях, когда статистика отсутствует можно использовать метод прямых наблюдений, формируя тем самым карту плотности заказов, как показано на рисунке
Или выполняя наблюдения за действиями операторов, формируя диаграмму спагетти. Каждый из приведенных методов, помогает выявить недостатки в размещении хранения грузов.
Еще один метод группировки - это совместное хранение “товаров-попутчиков”. Материалы, которые были заказаны и привезены вместе, должны храниться тем же образом.
Идея 8: Повышайте надежность сбора товаров для заказа
Надежность сбора и минимальное количество ошибок – это направление, в котором даже эффективные по многим пунктам склады могут потерпеть неудачу. Ошибкам нужно уделить много внимания. При сборе не тех материалов склад имеет потери не только на возврат закупки, но и на возврат запасов на место. Использование автоматических систем проверки и недопущения отгрузки в случае несоответствия штрих кода товара либо информации в накладной, должно придать больше надежности и контролируемости выполняемым действиям. Ну а каждая ошибка должна подвергаться анализу и внедрению действий, направленных на недопущения повторения в будущем.
Идея 9: Погрузка товара в обратном порядке к последовательности разгрузки.
Что касается этих операций, машины должны быть загружены в обратном порядке, чтобы последняя деталь была первой на разгрузку. Это позволит повысить эффективность последующих стадий логистической цепи.
Идея 10: Введите планирование отгрузки.
Это простой и эффективный способ поднять как скорость работы склада, так и эффективность использования транспорта. Знание последовательности отгрузок позволит лучше оптимизировать работу погрузчиков и их загрузку (подготавливая грузы сразу для нескольких машин, отгружаемых в ближайший час). Стандартизация действий при подготовке машины к погрузке означает не только точное время операции, но и все действия, которые могут быть выполнены до начала погрузки, сокращая тем самым цикл, выполняемых работ при погрузке товара.
Одна из глобальных проблем складов, как и большинства предприятий, где человеческий фактор играет важную роль - это, конечно, кадры. Большинство фирм испытывают острую нехватку персонала, а среди кладовщиков, операторов и грузчиков наблюдается большая текучка - редко люди, особенно молодые, задерживаются на такой работе больше одного - двух лет. Сложности работы со старшим поколением, в том, что им тяжело постичь работу компьютерных программ по учету ТМЦ и упаковочного оборудования. Так как же быть?
В первую очередь, необходимо отдавать себе отчет в том, что склад это одна из самых значимых частей бизнеса - склад не тратит деньги, он их зарабатывает!
Для того, чтобы не было текучки кадров, необходимо не только платить людям достойные зарплаты, но и использовать инструменты для формирования морального настроя сотрудника на складе. Для проверки материальной составляющей можно сравнить расходы по недостачам и порче материальных ценностей в разные периоды работы склада - когда число опытных рабочих превалирует над вновь поступившими и наоборот. Иногда потери от ошибок необученных или неопытных сотрудников, составляют больше, чем прибавка к зарплате старослужащему. А вот с моральными стимулами дело обстоит сложнее - их не всегда легко замерить.
Причина в том, что функционал работника склада ограничен определенным рамками и инициатива от него зачастую не требуется. Как же тогда заставить кладовщика или грузчика работать лучше?
Несомненно, необходимо не только ввести систему штрафов за опоздания, нарушения дисциплины, задержки при отгрузке и т. д., но и соответственно, если сотрудник не допускает нарушений, поощрять премией, выбирать в конце месяца лучшего сотрудника, объявлять благодарность и т. д. - это первое, что приходит на ум, тут, как говорится, подходят даже самые простые "советские" методы.
Однако, если рассуждать прогрессивно - появились ли о новые инструменты для управления и мотивации персонала на рынке труда?
Обратимся к опыту коллег:
Логистический оператор TABLOGIX, опираясь на свой 20-ти летний опыт в области управления складом, разработал и внедрил собственную систему индивидуальной мотивации сотрудников, получившую название 3С - Система Справедливого Стимулирования.
Система позволяет учитывать в сопоставимых условных единицах все виды складских работ, произведенных каждым работником, определять его суммарный трудовой вклад в общую копилку и перераспределять премию пропорционально этому вкладу. Таким образом, система стимулирования 3С поощряет тех работников, кто способен выполнить больше заданий с высоким уровнем качества, взяв на себя дополнительную нагрузку. Эта система предполагает формирование премиальной части на основе оценки 3 параметров: производительности труда , качества работы и лояльности работника .
С целью исключения субъективного фактора процесс оценки производительности полностью автоматизирован посредством разработки системы KPI, позволяющей в режиме реального времени рассчитать производительность работника в каждую минуту его рабочей смены. Зачастую на практике рост производительности влечет за собой снижение уровня качества. В связи с этим другим значимым параметром оценки работы стало качество. Оно рассчитывается по итогам расчетного периода на основе количества ошибок, допущенных работником. Помимо производительности и качества необходимо учитывать фактор добросовестного отношения к труду, который условно назвали «лояльность». Лояльность рассматривается, как готовность работника выполнять необходимые поручения руководителя, когда заданий по его основной специализации в данный момент нет. При формировании премии удельный вес показателя производительности составляет 50% , качества 40% , лояльности 10% .
Перечень оцениваемых работ включает все складские операции: разгрузка, погрузка, сортировка, размещение, пополнение, перемещение, отбор паллетами, отбор коробами, инвентаризация и т.п. Важно, чтобы абсолютно все виды работ, выполненные каждым работником, были учтены и получили свою оценку.
Данные о количестве выполненных заданий и затраченном на них времени, система импортирует из автоматизированной WMS-системы управления складом .
Наличие такой системы позволяет быть уверенным в заинтересованности персонала, который понимает, как происходит оценка труда. Это также позволяет определить возможность выполнения планов производства действующим штатом и обосновать изменения в бюджете для решения новых производственных задач. Заложив в настройки системы мониторинг производительности труда в режиме реального времени, руководитель получает информацию о производительности труда работников в каждую минуту их рабочей смены. Таким образом, он может немедленно реагировать на возможные отклонения, предпринимая корректирующие мероприятия, и в случае необходимости привлекать дополнительные ресурсы. При этом тревожные звоночки можно увидеть сразу, а не постфактум, по итогам уже ушедшего периода.
Как это работает на практике? Допустим за один час с 8:00 до 9:00, работник А – выгрузил 30 паллет, Работник Б – разместил 30 паллет, Работник С – осуществил подбор 30 линий, а работник Д – нигде и никем не был замечен. Каждое выполненное задание сотрудник подтверждает с помощью терминала сбора данных. Все данные отображаются в WMS, а учет произведенных работ осуществляет специальная программа, разработанная TABLOGIX. При введенных нормативах, например: разгрузки 1.5 мин на паллет, размещения товара на хранение в 1.8 мин и отбор строки заказа в 2 мин. мы получим следующие показатели активности работников (Коэффициент производительности – KPI):
Работник А: 30*1.5/60 = 0.75
Работник Б: 30*1.8/60 = 0.9
Работник С: 30*2/60 = 1.0
Работник Д: 0/60 = 0.
Из данных показателей мы видим, что работник С является самым продуктивным и выполняет все необходимые нормативы. Из этих же показателей мы можем выяснить на каком этапе работ у нас возникают сложности у большинства сотрудников - это позволит наиболее гибко распределять на складе человеческие ресурсы.
Коэффициент качества учитывает количество ошибок работника при подборе линий, выявленные технологические нарушения, выявленные случаи повреждения и брака и др. Если показатель качества соответствует установленным на складе требованиям, значит, работник заслужил вторую часть премии.
Лояльность – это, другими словами, старательность и добросовестность. Параметр лояльности позволяет избежать ситуаций, когда рабочий отказывается выполнять задания, которые напрямую не относятся к его непосредственным обязанностям.
Внедрение такой системы дало прирост производительности труда складских сотрудников на 30%, при этом значительно уменьшив количество брака.
Таким образом, внедрив автоматизированную систему учета индивидуальной мотивации сотрудника, руководство не только получило мощный инструмент для отслеживания эффективности трудовых ресурсов, но и позволила рядовым работникам прогнозировать размер своих вознагражданий через количество затраченных усилий на единицу рабочего времени.
Другие наши коллеги из логистического агенства “20А” творчески подошли к вопросу моральной мотивации сотрудников: вот уже почти два года на их складах звучит “функциональная музыка”.
Функциональная музыка (или музыка для производства) появилась более 80 лет назад. Монотонная работа на активно развивавшемся в то время конвейерном производстве требовала увеличения комфорта труда без ущерба производительности. Хорошим решением стало использование музыки. Ритмичная и при этом ненавязчивая музыка на подсознательному уровне помогает работать четко и слажено, снижая эмоциональную нагрузку и, соответственно, утомляемость. Музыка начала применяться еще на предприятии Генри Форда, получила большую популярность в СССР (особенно, на текстильных производствах), применялась НАСА при подготовке космонавтов. В 80-е-90-е годы ее популярность несколько снизилась, но уже в 2000-е годы это направление стимулирования получило новый импульс для развития за счет современных информационных технологий.
Несмотря на возможности современной автоматизации, основой логистического бизнеса остаются люди, выполняющие кропотливую и ответственную работу, которая сопряжена как с физическим трудом, так и с эксплуатацией достаточно сложной техники. В связи с этим музыкальный фон, должен быть умеренным, – мягко стимулирующим, не «навязывающим» такт и ритм работы.
Коллеги добились таким способом общего снижения стресса, конфликтности, повышения удовлетворенности трудом, снижения количества ошибок и травматизма, производительность выросла на 10%.
В наше время получение современного управленческого образования - не проблема. Многие руководители имеют степень МБА по управлению персоналом, подавляющее большинство менеджеров в крупных фирмах получили дополнительное образование в данной области. Кроме того, есть масса литературы для самообразования. Но вот что странно – несмотря на это, многие российские фирмы спустя 5-10 лет после своего появления, приобретают до боли знакомые «очертания» нашего совкового прошлого - бюрократизм, неповоротливость, затратность бизнес-процессов, низкий уровень корпоративной культуры и неспособность к изменениям.
В чём же причина? Рискем сказать – в нас самих. Не секрет, что в каждом из нас присутствует рудимент нашего исторического прошлого – этакий сталинский или “совковый” стиль управления. Не удивительно – три поколения советских менеджеров выросло на этой идеологии. Да и нынешние молодые руководители нередко в точности копируют навыки своих «учителей», считая их эффективными, поскольку ничего другого они просто не видели.
Как же быть? Ответ один – меняться. Выдавливать из себя “cовок” по капле, но каждый день. Примите всё нижеописанное как тест на заболевание «сталинизмом» и предложения, как это лечить.
1. Если в вашей фирме считается, что расследование проблемы закончено только если кого-то покарали, знайте – Вами правит “Совок”! Устраняйте системную причину. Если данное решение найдено, так ли уж важно сурово наказать «стрелочника» за ошибку, которая произошла в прошлом? Важнее привлечь к сотрудничеству исполнителей, которым это решение предстоит внедрять. Причём именно на стадии поиска решения. Если же сознание сотрудников будет «заторможено» страхом будущего взыскания, поверьте, результаты будут ничтожны. А вот озлобление и обида в головах останутся надолго… Разве эту цель ставят перед Вами собственники бизнеса?
2. Если в вашем подразделении количество штрафов (демотивация) превышает количество премий (мотивация) – значит, Вам пора отращивать усы и начинать курить трубку! Невозможно заставить людей эффективно работать с помощью угрозы. Мы это уже проходили! Двигать вперёд можно только выгодой. Это отнюдь не значит, что мы против взысканий и требовательности. Но количество и сумма поощрений должна быть в разы большей количества и сумм взысканий. Оцените свою систему мотивации с этой точки зрения и внесите изменения пока не поздно.
3. Формализм в поощрениях. Если в Вашей фирме награждения производятся только по «знаменательным датам», и вы не можете себе позволить оперативно «день в день» наградить отличившихся работников за значимое достижение, значит вашим персоналом начала править бухгалтерия или ОТиЗП… Верный признак «развитого социализма»! Система мотивации – это важнейшая часть современной технологии управления персоналом. Формализм может выхолостить из него все управленческие функции и превратить эффективный механизм просто в плановые затраты!
Необходимо не только слушать, но и слышать своих коллег и подчиненных, иначе рано или поздно столкнетесь с ситуацией, когда окажется, что для решения рабочего процесса будет предложена инновация, стоящая компании серьезных средств, а в итоге окажется, что вопрос на местах мог решиться вентилятором за 1500 рублей, как в старой байке про пустые тюбики .
Экспериментируйте и развивайтесь, поддерживайте инициативу и будьте инициативны. И помните, хороши любые изменения, если в конечном итоге они двигают вашу компанию вперед!
РАЗВИВАЕМСЯ ВМЕСТЕ!
На что смотреть.
Прежде, чем на складе можно будет что-то реально изменить, необходимо обеспечить соблюдение двух важных условий. Речь идет о точности информации о состоянии товара и о том, в каком конкретно месте склада он находится. Соответственно, это два направления работы:
1) работа с некондиционным товаром, включающая своевременное выявление брака и его отделение от качественного товара, повышение оперативности процессов учета и создание зоны брака (либо наведение порядка в имеющейся);
2) качественная инвентаризация. Если она проведена некачественно, буквально на следующий день снова начинаются проблемы с поиском товара, и склад начинает плавно снижать производительность.
Следует отметить при этом, что идеальное решение для инвентаризации – двойной слепой пересчет – довольно ресурсоемко, а решить проблему с помощью единственной, пусть даже супер-точной инвентаризации никак не получится. Для достижения устойчивого результата понадобится несколько инвентаризаций за период, со все более точной информацией по размещению и состоянию товара.
Чтобы устранить ситуации, когда сотрудники мешают друг другу работать, имеет смысл ввести простое правило: складская зона выделяется для выполнения определенной задачи и для устранения помех при выполнении других складских операций. В качестве примера можно привести простое решение: создание зоны стикеровки товара.
Можно, конечно, стикеровать товар на входе, но тогда не только потребуются дополнительные площади для приемки, но и приходование грузов будет задерживаться, замедляя движение по всей технологической цепочке. Можно производить стикеровку и на выходе, но при этом падает производительность отбора и снижается мощность склада по отгрузке (растет время от приема заказа до его выдачи). Кроме того, в периоды пиковых отгрузок будет либо игнорироваться стикеровка, либо расти количество опозданий.
В рассматриваемой ситуации было применено третье решение, тем более приемлемое, что на данном складе всегда есть запас товара на 3–4 дня отгрузки. Для стикеровки товара выделили отдельную зону и обеспечили раздельное хранение стикерованного и нестикерованного товара. Т.е. сразу после приемки товар идет в карантин, а уже после стикеровки поступает на отгрузку. При этом ни тот, ни другой процесс не замедляется, но требуется отдельная зона стикеровки и отдельная зона хранения карантинного (нестикерованного) товара.
Начинать оптимизацию процесса приемки следует с заблаговременного обеспечения склада информацией. Это подразумевает запрет на прием товара по бумажным документам поставщика и потребует выполнения всей подготовительной работы (в идеале – вплоть до создания приходной накладной) заранее. Тогда в самом начале отсекаются ошибки документооборота, устраняются задержки на создание артикула и прочие проблемы, связанные, например, с перепроводкой приема задним числом, опозданием товара и т.д. Однако главным преимуществом при этом является предварительное планирование размещения товара. Если на складе внедрена адресная система хранения, такое планирование становится вполне возможным.
Прием возвратного товара («недовозов» и возвратов от клиентов), несмотря на то, что на него приходится незначительный процент грузооборота, должен быть регламентирован максимально жестко и выполняться в минимальные сроки. Причина все та же – необходимо обеспечить качество информации о товаре. В данном случае – чтобы сократить потери времени отборщиков на поиски «редких» позиций, которые числятся в возвратах, но не были своевременно размещены на складе.
Интересным инструментом оптимизации системы размещения может стать применение категоризации товаров. Для этого нужно ввести ABCXYZ-категоризацию в информационную систему склада (в справочник товаров или создать отдельный справочник) и при планировании размещения выполнять в качестве первого шага сортировку строк приходной накладной по данному признаку. Благодаря этому процесс размещения упрощается и становится доступным кладовщику средней квалификации – достаточно выполнить сортировку не по артикулам, а предписанной командой по категориям, и после этого размещать строчки сверху вниз. В результате товар категории АХ будет размещен максимально близко к месту отбора (при наличии свободных ячеек). И даже если на складе имеется дефицит площадей, он отразится, в первую очередь, на товарах категории С.
Следует отметить, что заниматься оптимизацией размещения и минимизацией внутрискладских перемещений персонала и техники необходимо еще при планировании размещения товара на складе. Если изначально правильно укомплектовать «горячую зону» отбора, то уже при внедрении описанных выше организационных можно получить довольно ощутимый эффект.
Важнейшей задачей оптимизации перемещений является сокращение вынужденных простоев. Наибольший эффект в данном случае приносят два инструмента – управление волнами заказов и расстановка приоритетов складских работ.
Управление волнами заказов – прекрасный инструмент «борьбы с хаосом» на складе, который, к сожалению, применяется далеко не так часто, как хотелось бы. При том, что единого алгоритма создания волны на любом складе нет и быть не может, общая логика такова: любое принятое в конкретном случае правило лучше, чем их полное отсутствие, и принесет значительный положительный эффект. В первую очередь, это будет касаться выравнивания нагрузки и уменьшения вынужденных простоев на разных (прежде всего, смежных) участках технологической цепи – к примеру, при пополнении зоны отбора, собственно отборе и контроле заказов.
В качестве примера можно привести простое правило: если из системы одновременно поступает 10 заказов, отбор нужно начинать с самых маленьких из них. Что это даст? Во-первых, работа будет быстрее передана на следующий участок, т.е. на контроль (уменьшится время простоя на следующем участке работы). Во-вторых, это выровняет нагрузку на работников, которые занимаются пополнением товара и внутрискладскими перемещениями..
Что касается второго инструмента, то на многих складах приоритеты внутрискладских перемещений, расставляются по клиентам (собственные заказы, VIP-клиенты и т.д.). Но система будет работать гораздо эффективнее, если определять приоритеты заданий по векторам перемещения товаров в складе, настраивая их в складской системе учета по зоне-источнику и зоне-приемнику.
В рамках этой логики очевидно, что самой важной складской работой будет пополнение зоны отбора (чтобы отборщики не простаивали), а наименее важной – перемещение товара внутри зоны отбора (по каким бы то ни было соображениям).
В случае, который уже приводился в пример, в процессе внедрения исходного варианта расстановки приоритетов появлялись дополнительные зоны стикеровки и переупаковки. Для них также были расставлены приоритеты работы. При этом перемещение из зоны стикеровки в любую другую получило один из самых высоких приоритетов, поскольку Если не будет стикерованного (точнее готового к отгрузке товара) – нечего будет «загрузить» во внутрискладские перемещения.
Наиболее очевидный инструмент оптимизации на этом участке – аппаратный контроль результатов работы во избежание дальнейших «разбирательств» с клиентами, связанных с допущенными ошибками. Организационные приоритеты здесь имеет смысл выстроить в таком порядке:
1. жесткое соблюдение поставленных сроков. Машина, отгруженная качественно, но с опозданием, может попросту вернуться, поскольку не успеет довезти и сдать товар, и окажется, что всю работу сделали зря;
2. качество проведения работ;
3. производительность, которая не должна наращиваться в ущерб двум первым параметрам.
Основная цель, к которой нужно стремиться на этом участке – именно уменьшение трудозатрат на исправление ошибок и урегулирование проблемных ситуаций, актов несоответствия и т.д. Ведь даже по самым приблизительным подсчетам 1 час некачественной работы контролера может обойтись компании в порядка 6 часов дополнительного рабочего времени на исправление ошибок (– напереписку с клиентами, проведение выборочных инвентаризаций и т.д., и т.п.) Поэтому гораздо проще и дешевле сразу обеспечить необходимые условия для качественного контроля.
Результаты
В реальной ситуации, практические примеры из которой приводились выше, через 2 месяца после начала работ по оптимизации бизнес-процессов были достигнуты следующие результаты.
- Срок приемки товаров был сокращен вдвое.
- Производительность отборщиков выросла на 25%, а общая производительность складских операций – на 36% (оценено по результатам нормирования складских операций на старте проекта и через 2 месяца).
- Эффективность транспорта доставки выросла на 21%. Изначально данному параметру внимание не уделялось, изменения произошли за счет роста загруженности на рейс, снижения общего пробега, уменьшения процента возвратов на склад.
- Брак склада был уменьшен на 74%. Изменилась ситуация, когда за брак в течение смены никто не нес ответственности, и, соответственно, отношение работников к товару.
Василий ДЕМИН,
руководитель проекта «Складская логистика»
Координационного совета по логистике
В данной публикации мы рассмотрим методы оптимизации четырех взаимосвязанных стадий складского технологического процесса: идентификацию поступившей продукции, размещение товаров на хранение и комплектацию заказов.
I . Идентификация . Безусловно, нет необходимости объяснять значимость такой операции, как идентификация поступающей продукции. Без проведения данной операции любой склад просто «задохнется», так как в дальнейшем невозможно будет осуществлять ни учет и контроль за движением и состоянием продукции на складе, ни его поиск при проведении комплектации и инвентаризации. Однако к выбору метода идентификации следует подходить, тщательно взвесив задачи, стоящие перед складом, его технико-технологические и финансовые возможности, природу товарного ассортимента и многое другое. В своей практике мы встречали объекты, в которых идентификация практически не производилась вообще, точнее к периодически присутствующим ярлыкам производителя на коробах и паллетах грузчики подручными средствами «дорисовывали» одним им понятные символы и обозначения, что естественно в дальнейшем приводило к путанице. Как правило, данную проблему пытались разрешить резким, необдуманным введением штрихового кодирования, что в 80 процентов случаев приводило к неэффективным затратам, так как данные склады изначально не были подготовлены к внедрению штрихового кодирования и не имели технико-технологических возможностей для выполнения данных операций, не было подготовлено должное программное обеспечение и т.д. Эффективность операций по идентификации продукции на данных складах сводилась к нулю. В связи с этим мы рассмотрим три основные метода идентификации в складском технологическом процессе, каждый из которых может быть эффективен в зависимости от возможностей конкретного склада, целей и задач, стоящих перед ним.
1. Индивидуальное кодирование . Это наиболее примитивный метод идентификации, при этом предполагающий минимальное количество затрат на его внедрение и использование. Сущность индивидуального кодирования заключается в следующем: каждой товарной позиции присваивается индивидуальный код, который может содержать в себе информацию («смысловой» код), так и не нести никакой информации («несмысловое» кодирование). При разработке «смыслового» кода необходимо определить, какая информация является важнейшей и требует сохранения в коде. Например, создается девятизначный код, который включает в себя информацию о поставщике (первые 3 цифры), информацию о товарной группе (2 цифры) и товарной позиции (3 цифры), о статусе данного товара (например, о его ценности, порядке хранения и пр.). Пример структуры индивидуального смыслового кода приведен на рисунке 1.
Рис. 1. Пример структуры индивидуального смыслового кода
Абсолютно не обязательно наличие знания структуры кода оперативными работниками: грузчиками, комплектовщиками и т.д. - важно, чтобы структура кода и значение каждой цифры были зафиксированы в нормативном документе предприятия, и руководитель склада, его заместители или другие лица при необходимости всегда могли определить информацию по конкретной грузовой единице. Основной целью данного вида идентификации является возможность учета продукции на складе, ее индивидуализации при комплектации заказов. Аналогичную функцию носит и «несмысловое» кодирование, когда каждой товарной позиции присваивается свой индивидуальный номер, что позволяет индивидуализировать ее среди другой продукции при однородном внешнем виде.
Стоимость внедрения и использования данного метода невысока. Как правило, в затраты на введение индивидуального кодирования включается только закупка этикеточной ленты и печать на ней кодов товаров, а также закупка нескольких этикет-пистолетов.
Ярлык (этикетка) с напечатанной на ней кодом товарной позиции наклеивается с помощью этикет-пистолета на каждую грузовую единицу, после завершения операций по приемке продукции и ее сортировке.
2. Штриховое кодирование (ШК ). Внедрение ШК на складе позволяет существенно ускорить процесс приемки продукции (в случае, если на поступающих грузовых единицах уже имеется штрих-код), значительно снизить риск «человеческих» ошибок в процессе выполнения технологических операций и при проведении инвентаризации, а также упростить поиск (определение) нужного товара на стеллаже или в стеллажной ячейке. Внедрение ШК также обосновывается и тем, что все чаще крупные клиенты торговых и производственных компаний ставят обязательным условием при закупках продукции наличие штрих-кода. Однако внедрение системы ШК влечет за собой достаточно серьезные прямые и косвенные затраты. К прямым затратам относится закупка оборудования (терминалы сбора данных, сканеры, сервер, принтер для печати этикеток), программного обеспечения, совместимого с системой ШК, оплата услуг и взносов в Ассоциацию Юнискан EAN. К косвенным затратам можно отнести обучение персонала, услуги консультантов по подготовке склада к внедрению ШК и пр.
3. Радиочастотная идентификация (RFID ). Система RFID появилась сравнительно недавно и в настоящее время на российских складах практически не используется. Однако успешный опыт внедрения данной системы рядом крупных компаний в Европе (в частности Италией и Германией) позволяет делать выводы о том, что в среднесрочной перспективе широкое применение системы RFID начнется и в России.
Система RFID состоит из трех элементов - метка (tag), антенна (reader) и компьютер.
Работа системы. В метку заносятся необходимые данные о грузовой единице, после чего данные метки могут передаваться в компьютер с помощью антенны.
Преимущества RFID :
- данные идентификационной метки могут изменяться и дополняться;
- на метку можно записать гораздо больше данных, по сравнению с штрих-кодом;
- данные на метке могут быть засекречены;
- радиочастотные метки более долговечны;
- расположение метки не имеет значения для считывания (метка может находиться внутри короба или паллеты);
- метка лучше защищена от воздействия окружающей среды;
- метки могут иметь многоразовое использование;
- при использовании RFID появляется возможность контроля за перемещениями груза.
Недостатки RFID :
- относительно высокая стоимость;
- невозможность размещения под металлическими и электропроводными поверхностями;
- подверженность помехам в виде электромагнитных полей;
- локальное использование RFID.
II . Размещение товаров на хранение необходимо производить таким образом, чтобы при последующих технологических операциях количество перемещений складских служащих было минимальным. С этой целью производится деление всех товарных позиций на 3 группы, после чего для их хранения выделяются «горячие» и «холодные» складские зоны. Для того чтобы произвести оптимальное деление всей номенклатуры, необходимо воспользоваться методикой ABC, XYZ анализа. В данном случае, т.е. применительно к технологическому процессу, основным критерием деления товарных позиций на группы будет выступать количество подходов/перемещений складского персонала при выполнении технологический операций, в частности, при процедуре комплектации заказов в производство или клиентам.
Таблица 1. ABC анализ товарных позиций
? | Код(артикул) | Количество заказов | Группа | |
1 | Степлер SAX 49 | 1238 | 455 | А |
2 | Степлер SAX 51 | 1245 | 410 | А |
3 | Ручка Senator Spring | 4589 | 398 | В |
4 | Ручка Pilot BPGP-10R-F | 4593 | 355 | В |
5 | Ручка Parker Sonet | 4599 | 223 | В |
6 | Ручка Parker Insignia | 4600 | 131 | С |
7 | Ручка Parker Frontier | 4611 | 110 | С |
8 | Ручка Ico Omega | 4678 | 95 | С |
9 | Тонер-картридж HP C71 1 5X | 5889 | 23 | С |
10 | Тонер-картридж HP C8061A | 5890 | 4 | С |
Таблица 2. XYZ анализ товарных позиций
? | Наименование товарной позиции | Код (артикул) | Кол-во отгруженных универсальных коробов | Группа |
1 | Тонер-картридж HP C8061A | 5889 | 1800 | X |
2 | Степлер SAX 51 | 1245 | 1550 | X |
3 | Ручка Parker Insignia | 4600 | 580 | Y |
4 | Ручка Senator Spring | 4589 | 530 | Y |
5 | Ручка Ico Omega | 4678 | 525 | Y |
6 | Ручка Pilot BPGP-10R-F | 4593 | 335 | Z |
7 | Степлер SAX 49 | 1238 | 325 | Z |
8 | Тонер-картридж HP C71 15X | 5890 | 305 | Z |
9 | Ручка Parker Frontier | 4611 | 123 | Z |
10 | Ручка Parker Sonet | 4599 | 115 | Z |
Для проведения ABC, XYZ анализа необходимо собрать статистические данные, предпочтительно, не менее чем за предыдущий год. Информация должна содержать: наименование по каждой товарной позиции, количество заказов и количество отгруженных универсальных грузовых единиц помесячно по каждой товарной позиции. После составления статистической базы производится деление всего товарного ассортимента по ABC анализу на три группы. Как правило, деление производится в классических пропорциях: группа А - 20 процентов, группа В - 30 процентов, группа С - 50 процентов. Критерием деления ABC анализа является количество заказов по каждой товарной позиции. Пример деления товарных позиций по ABC анализу см. в таблице - 1.
Таким образом, в группу А вошли 20 процентов товарных позиций (степлер SAX 49 и степлер SAX 51), которые встречались в заказах чаще всего; в группу В - 30 процентов товарных позиций, которые встречались реже, и в группу С - 50 процентов товарных позиций, которые встречались в заказах гораздо реже по сравнению с первой группой. На первый взгляд, можно сделать вывод о том, что наибольшее количество подходов/передвижений будет осуществляться к позициям группы А, однако это не совсем так, ведь необходимо учесть еще и такой критерий, как количество отгружаемой продукции. Несмотря на то что заказов на такую позицию, как «тонер-картридж HP С8061А», было всего четыре, количество отгруженных коробов, а, следовательно, и количество подходов к месту хранения этого товара могло быть гораздо больше.
Рассмотрим методику проведения XYZ анализа, критерием деления в котором будет количество отгруженных универсальных единиц. Пропорциональное деление аналогично делению при проведении ABC анализа, т.е. 20/30/50 процентов. Пример деления товарных позиций по XYZ анализу см. в таблице - 2.
Таблица 3
Для того чтобы решить конечную задачу о размещении товаров в «горячие» и «холодную» зоны, необходимо составить матрицу результатов ABC, XYZ анализа (см. таблицу - 3). Обычно сопоставление результатов проведенного анализа производится в MS Excel с помощью функции сортировки и занимает минимальное количество времени, в данной же публикации мы представим матрицу в виде таблицы (см. таблицу - 3).
Таким образом, после расстановки всех позиций по соответствующим категориям можно сделать вывод, что к «горячей» зоне хранения будут отнесены позиции, находящиеся в квадратах АХ, AY, BX (в данном случае только одна позиция с кодом 1245), к «средней» зоне хранения - позиции, находящиеся в квадратах AZ, BY, CX, и к «холодной» зоне хранения -позиции, находящиеся в квадратах BZ, CZ, CY.
При проведении ABC, XYZ анализа следует придерживаться, по крайней мере, двух правил: первое - статистические данные должны быть взяты не менее чем за предыдущий год с разделением по кварталам и месяцам, т.к. именно в течение всего годового цикла можно выделить сезоны спроса по каждой товарной позиции и размещать продукцию по зонам хранения не статично весь год, а перемещать ее между зонами в соответствии с сезонностью спроса; второе - единицы измерения должны быть унифицированы. Если на склад продукция приходит и хранится, допустим, в 15 видах различных коробов, следует измерить геометрические параметры каждого из них и выбрать размеры унифицированного короба, в котором и будет измеряться количество отгружаемой продукции.
Рис. 4.
Схема комплектации заказа
После проведения ABC, XYZ анализа вычисляется норма запаса по каждой товарной позиции, находящаяся на складе единовременно, далее определяется количество мест хранения для каждой товарной позиции и производится размещение на основе проведенного анализа. «Горячая» зона, как правило, располагается ближе к зоне отгрузки, на стеллажах, находящихся в центральном проезде, в нижних ярусах стеллажей. Данное размещение позволяет существенно сократить время на выполнение технологических операций (размещение на хранение, комплектацию и т.д.). Следует также отметить, что в настоящее время большинство информационных систем класса ERP или WMS имеют функцию проведения ABC, XYZ анализа по различным задаваемым критериям.
Второй задачей при размещении продукции на хранение является оптимальное разделение складских запасов. Безусловно, оптимальным является такой вариант, когда весь товарный запас хранится на стеллажах (исключая наливные, насыпные и «негабаритные» грузы), при котором отбираемый запас находится в нижних ярусах стеллажей, а резервный в верхних.
Однако склады с недостаточным финансированием, часто не имеют возможности приобретения стеллажного оборудования для хранения всего товарного запаса. Для складов данной категории возможно применение варианта с разделением товарного запаса на две категории и хранение их в двух зонах. В зоне отбираемого запаса на стеллажах хранится только минимальный одно-двухдневный запас по каждой товарной позиции, в резервной зоне хранения весь оставшийся запас хранится штабельным способом. Пополнение запаса отбираемой зоны хранения производится, как правило, в третью смену с целью упразднения пересечения потоков. Применение данного способа позволяет в несколько раз сократить количество стеллажного оборудования и сократить площадь комплектации, а, следовательно, и количество перемещений между местами отборки.
Рис. 5. Зональное деление склада при комплексной сборке заказов
III . Комплектация заказов . На большинстве складов оптовых торговых и производственных предприятий, а также на складах логистических центров данная операция является ключевой, так как именно от нее зависит уровень логистического обслуживания (скорость выполнения заказа, отсутствие ошибок при сборе и т.д.). При этом данная операция является одной из трудоемких в складском технологическом процессе.
Существует две системы выполнения технологических операций по комплектации: «человек к товару» и «товар к человеку».
Система -товар к человеку? является полностью автоматизированной (см. рис. 3). Управление передвижением товара осуществляется оператором при помощи пульта управления, при этом сам оператор не производит никаких перемещений, товар поступает к окну выдачи автоматически. В настоящее время применение таких систем в России нашло небольшое применение.
Система -человек к товару? . По результатам хронометража работы комплектовщика, проводимого на 23 складах предприятий оптовой торговли, были получены следующие усредненные результаты: 50 процентов времени комплектовщика расходуется на перемещение между местами отборки, 20 процентов - вынужденный простой (ожидание), 20 процентов - работа с документами, 10 процентов - изъятие с места отборки. Однако существуют методы оптимизации процедуры комплектации, при применении которых сокращается общее время сборки заказа за счет полного упразднения простоя и сокращения времени на перемещения между местами отборки.
Рассмотрим типовую схему процесса комплектации заказов (см. рис. 4.)
1. Процедура комплектации начинается с получения накладной на отпуск товара (заявка, лист комплектации и т.д.), обязательным условием является расположение в документе товарных позиций в соответствии с размещением продукции на складе, иначе образуется ситуация, когда накладная составляется в таком порядке, в котором она существует в информационной системе, и комплектовщик вынужден совершать неэффективный путь, то есть неоднократно возвращаться к ранее пройденным местам и т.д.
2. Составление маршрутной карты. В работе большинства складов данная процедура не используется совсем. Однако оптимальное составление пути движения комплектовщика позволяет существенно сократить время на сборку заказа. Критерием составления маршрутной карты будет являться не только размещение адресов нахождения товара в соответствии с их расположением на складе, но и, что более важно, учет принципа «товарного соседства». Например, на складе компании, занимающейся оптовой продажей канцелярских товаров, комплектовщике платформенной тележкой отбирает в соответствии с заказом несколько видов ватмана, после чего у него в листе комплектации находится позиция -Бумага для принтера «Снегурочка», это приводит к тому, что комплектовщик вынужден тратить значительное время на перекладку товара в тележке, кроме того, как правило, данная пересортировка производится в неподготовленных условиях (пыль от бетонного пола и пр.), что часто приводит к нарушению внешнего вида упаковки.
3. Отборка груза с мест хранения.
4. Комплектация собранного заказа, его упаковка и маркировка.
Дифференциация в выполнении последних двух операций будет зависеть от вида комплектации - индивидуальной или комплексной. Индивидуальная комплектация заказа заключается в последовательной отборке одного заказа одним сборщиком. Комплексная комплектация - сборка одного заказа по частям разными комплектовщиками в отдельных секторах склада. При индивидуальной сборке комплектовщик вынужден проходить значительные расстояния, а, следовательно, и затрачивать большое количество времени при перемещениях между местами отборки, кроме того, возрастает вероятность пересечения потоков, а, следовательно, возникновения ситуаций ожиданий освобождения технологической зоны другими служащими.
Комплексный способ сборки заказов более эффективен. При таком способе склад разделяется на несколько зон в каждой, из которых работает один комплектовщик. При этом геометрические размеры зон могут быть различны, важно рассчитать одинаковое количество операций, приходящееся на каждую зону, а точнее время для их выполнения. Например, зона - 7 по геометрическим параметрам будет значительно меньше, чем зона - 1, однако она находится на значительном удалении от зоны приемки/разгрузки, а, следовательно, и время на выполнение операций по доставке заказа будет больше и т.д. Пример зонального деления приведен на рисунке 5.
Поступивший заказ разделяется на части, соответствующие зонам склада. После сборки в каждом участке собранная часть передается на участок приемки в квадрат, номер которого обозначен в листе комплектации у каждого комплектовщика, собирающего единый заказ. После сборки всего заказа кладовщик проверяет правильность собранного заказа, далее производятся предотгрузочные операции. Преимущества данного метода очевидны: во-первых, скорость выполнения заказа сокращается в несколько раз, за счет сокращения количества перемещений между местами отборки и упразднения вынужденного простоя; во-вторых, каждый комплектовщик, «прикрепленный» к конкретной зоне, гораздо быстрее узнает номенклатуру, хранящуюся в ней и фактически имеет возможность работать без маршрутного листа; в-третьих, появляется возможность закрепления индивидуальной ответственности за состоянием каждой складской зоны. Минусом данной системы некоторые руководители складов называют возможность внезапного невыхода на работу части складского персонала и отсутствие в зоне комплектовщика. Однако это уже вопрос административно-организационный, большинство руководителей крупных складов, вводящие данную систему, смогли справиться с данным негативным фактором методами мотивации и административных взысканий. Во всяком случае, остается возможность «аварийной» переброски персонала из другой зоны.
Сергей Бубнов, Управляющий партнер компании Bestlog, Москва; кандидат экономических наук
- Как проанализировать и оптимизировать склад
- На какие узкие места обратить внимание в первую очередь
- Как быстро навести порядок на складе
- Как провела оптимизацию склада компания «Декёнинк Рус»
- Какие меры позволили компании «Совтрансавтоэкспедиция» увеличить оборот по складским операциям более чем на 30%
В деятельности практически любой компании может обнаружиться узкое место, из-за которого снижается производительность всей логистической системы. Часто таким проблемным звеном становится склад, причем как внешняя, так и внутренняя его инфраструктура. В этой статье я дам рекомендации по выявлению проблем, оптимизации склада и наведению порядка.
Типичные недостатки внешней инфраструктуры связаны со следующими элементами логистической системы и аспектами работы (см. также: Как оптимизировать работу склада и выявить узкие места в его работе) :
- дороги, проезды (в том числе пожарный), заезды, экстакады, рампы, докшелтеры (системы герметизации проема между стеной складского помещения и кузовом транспортного средства), доклевеллеры (устройства для выравнивания уровня пола здания с уровнем пола автофургона) и пр.;
- конфигурация земельного участка и складского комплекса, неудобные стоянки для автотранспорта, наличие разворотной площадки;
- расположение и конфигурация вспомогательных складских объектов (котельная, административно-бытовой комплекс, зарядная комната, резервуары для воды и пр.).
Узкие места внутренней инфраструктуры, как правило, обусловлены следующим:
- неподходящая частота сетки колонн, высота потолков на складе, наличие мезонина, нагрузка на пол склада, уровень пола склада и рамп и пр.;
- несовершенная складская технология в части приемки, маркировки, хранения, комплектации, набора, а также отгрузки продукции;
- неподходящие специализированные механизмы, оборудование, приспособления, используемые на складе (например, устройства захвата груза).
Приведу пример из практики. В марте 2013 года одному из наших клиентов потребовалось найти новую площадку для аренды. За месяц исследовали рынок существующих складских предложений в Московской области. В результате из 38 предложений 25 были отсеяны – в основном из-за неправильной сетки колонн (7 предложений) и низкой высоты потолка склада (10 предложений). Хотя такие складские комплексы сдаются по среднерыночной цене, включающей базовую арендную ставку, сумму налогов и коммунальных платежей, из-за непродуманных складских технологий арендаторы в дальнейшем вынуждены нести до 15–20% дополнительных логистических издержек ежемесячно, пытаясь самостоятельно исправить недочеты внешней и внутренней инфраструктуры арендуемого склада.
Оптимизация работы склада производится в три этапа.
- Организация хранения на складе готовой продукции: практические советы
Оптимизация склада: 3 этапа наведения порядка
Этап 1. Анализ склада и материальных потоков компании
Для его проведения нужно определить текущее состояние материальных потоков и сформулировать прогноз на будущее. В первую очередь следует анализировать:
- принадлежность товара к товарной группе (вид товара);
- запас товара (в штуках), причем как минимальный, так и максимальный;
- стоимость запаса товара (в рублях) – как минимального, так и максимального;
- вместимость палет (в штуках товара);
- количество палет (в штуках);
- прогноз максимального роста объема товаров (по количеству палет);
- размер поддона товара;
- вес, высота и другие характеристики палеты.
Этап 2. Оценка взаимодействия склада с другими подразделениями
Складские работники постоянно контактируют с сотрудниками отделов продаж, маркетинга, логистики и сервиса. Очень часто информационный разрыв в цепочке взаимодействия подразделений продаж, логистики и маркетинга приводит к образованию различающихся ассортиментных матриц в каждом подразделении, что в дальнейшем ведет к двойному учету, избытку или дефициту продукции на складе.
Чтобы понять, слаженно ли работают все службы, нужно сделать следующее.
- Опросить руководителей и работников склада, выяснить, какие проблемы и трудности у них возникают при взаимодействии со смежными отделами (IT, маркетинга, продаж, бухгалтерией, финансовой службой и производством). Например, между отделом маркетинга и складом часто возникают споры относительно учета, наличия, использования, регулярности уценки и утилизации рекламных образцов.
- Установить зоны ответственности сотрудников за складскую логистику по всем видам товарных запасов. Можно взять за основу так называемый цикл Деминга (модель непрерывного улучшения процессов PDCA, от англ. Plan – Do – Check – Act, «планируй – выполняй – проверяй – корректируй»). К примеру, возьмем отдел закупок. Оцените, насколько четко и сбалансированно распределены работы и ответственность сотрудников, проанализируйте проблемы. Подумайте, как можно организовать бесперебойное поступление закупаемых материалов на склад, как проконтролировать их приходование, провести анализ остатков и оборачиваемости товаров на складе.
- Оценить влияние каждого смежного отдела на потерю производительности работы склада. Например, в одной компании невнимание IT-службы к потребностям склада приводило к еженедельным восьмичасовым потерям производительности: не функционировали принтеры и периферийные устройства, с перебоями работали Интернет и учетная система.
- Определить объемы и периодичность поступления входящих, исходящих и возвращаемых грузов. Цифры, которые должны получиться в результате, расскажут Вам о частоте, характере и общей пропускной способности склада при получении грузов, их переработке, а также о возможности отгрузки. Приведу пример. Всего за сутки на склад поступает три фуры с грузом, при этом перерабатывается и отгружается лишь десять «газелей». Это может говорить о том, что по каким-то причинам происходят сбои в отгрузке, на которые нужно обратить внимание.
- Определить исходную причину потери производительности склада и принять меры для ее устранения. Например, в одной торговой компании эту роль сыграл тот факт, что товарный учет в ERP-системе вели сотрудники отдела продаж. Они сами не находились на складе, не были материально ответственными за приход товара, и все это не препятствовало хищениям. После того как в компании провели логистический аудит, работа была полностью перестроена. Так, учетную функцию передали складским работникам, которых сделали материально ответственными за товар. Отдел продаж разделили на две части: продающую и поддерживающую. Впоследствии вторую часть также решили отнести к службе логистики (в которую входит склад). Кроме того, склад оснастили видеокамерами во всех зонах: погрузка, выгрузка, входы, выходы, зона комплектации и дальние участки склада.
Этап 3. Анализ работы самого склада
Очень важно оценить работу склада с точки зрения оборачиваемости товара (то есть уровня запасов и занимаемой площади). Анализ этого параметра позволит понять, насколько быстро на складе осуществляются основные операции (приемка, отгрузка, сортировка продукции). К примеру, загруженность склада по ячейкам более чем на 90% приводит к потере производительности на 15% из-за трудностей с поиском грузов и места для размещения вновь пришедшего товара.
Кроме того, отсутствие четкого временного плана приемки и обслуживания заказов приводит к огромным потерям в производительности.
- Пути повышения экономической эффективности производства: 3 совета
Стоит обратить внимание еще на ряд моментов.
1. Параметры внешней и внутренней инфраструктуры. Так, на одном складе одинаковый с улицей уровень пола делал невозможной быструю механизированную отгрузку товара (идеальный вариант – ситуация, когда пол склада поднят на уровень от 1000 до 1200 мм от земли (улицы), чтобы после парковки фуры в док пол прицепа находился на одном уровне с полом склада). Другие примеры: частая сетка колонн (6 × 6 м, 7 × 7 м, 10 × 10 м), разбитый и слабый (в отношении выдерживаемой нагрузки) пол склада, небольшая высота помещения (до 5 м) затрудняют рациональное размещение стеллажного оборудования и оптимизацию внутреннего пространства склада. Плохо спланированные системы освещения, вентиляции, отопления и кондиционирования склада также приводят к потерям производительности. Неправильно установленное оборудование в доках приводит к очень значительным потерям тепла, если приемка и отгрузка малотоннажного транспорта происходят там же, где разгружаются большегрузные машины.
Что касается внешней инфраструктуры, то довольно часто недостаточное количество доков приводит к потерям от простоя транспорта в очереди перед складом.
2. Системы идентификации: надпись, штрихкод, радиочастотный идентификатор (RFID). Отсутствие системы идентификации палет может привести к частым проблемам с возвратами продукции, ошибкам в формировании заказов, а также к истечению сроков годности продукции. Если не применяется разделение труда и не используются специальные приспособления при маркировке, демаркировке, идентификации и упаковке продукции, это тоже замедляет работу склада.
3. Все закоулки склада. Они, как правило, заняты неликвидами, упаковкой, старьем, остатками выставочных образцов продукции и прочими ненужными вещами. Много неликвидов появляется, если плохо налажены система учета и работа с возвратами и претензиями, а также если на складе нет ротации продукции (годная продукция стареет и становится неликвидом).
На складе должны быть определенные зоны для хранения каждого вида продукции. О беспорядке часто говорит несоблюдение принципов ее хранения в закрепленной зоне, а также отсутствие системы визуального обозначения товара (это приводит к более чем 25-процентным потерям общей производительности склада). Одна из применяемых на практике систем такова:
- зеленый цвет – проверенный и годный товар;
- желтый – неопределенный статус;
- красный – брак.
4. Работа механизмов и оборудования. Известен случай, когда на складе компании было занято более 80% ячеек стеллажей. Из-за увеличения товаропотока руководству компании было рекомендовано перейти на узкопроходную технологию (применение специализированной техники с минимальным расстоянием между стеллажами), докупить фронтальные стеллажи, перепрофилировать существующую технику (электропогрузчик был переведен из зоны хранения в зону отгрузки). Реконструировали рампу, переставили стеллажи и увеличили количество постов отгрузки для малотоннажного транспорта. В результате на складе удалось разместить в два раза больше товара, увеличить быстроту отгрузки и число отгружаемых заказов в четыре раза.
- Вместимость склада: как увеличить полезную площадь на 60%
Как быстро провести операционные улучшения и оптимизировать склад
- указать ожидаемые окна отгрузки для постоянных клиентов;
- разграничить время отгрузки и самовывоза.
Суть второго мероприятия в том, чтобы разделить время прибытия транспорта под погрузку и самовывоз. Именно самовывоз, как показывает практика, вызывает до 80% всех проблем с отгрузкой на складе.
Чтобы лучше контролировать процесс улучшений, полезно составить план-график, в котором будут указаны возможная сумма затрат и ответственные лица (см. таблицу). Затем стоит проводить еженедельные совещания, чтобы контролировать соблюдение графика, а раз в месяц выезжать на склад вместе с теми, кто участвует в процессе (включая руководителей служб закупок, продаж, безопасности и бухгалтерии).
Улучшения обязательно должны быть увязаны со стратегией логистики, принятой в компании. Например, это может быть внедрение автоматизированной системы управления запасами товара. Такая система позволяет одновременно прогнозировать объем продаж и управлять процессом заказа товара у поставщика с учетом минимизации оборотных средств, использования складских площадей, расходов по доставке. С помощью такой системы можно также нормировать остатки продукции на складе.
Стратегические улучшения могут стать основой для инвестиционных предложений по кардинальному улучшению складской логистики в компании. Один из примеров – образование единого сервисного центра компании с филиальным разделением по региональным складам, обеспечивающим не только прием, обработку заказов, хранение, комплектацию и отгрузку продукции, но и обслуживание в части возвратов, претензий, обмена и выполнения гарантийных работ для оптовых и розничных клиентов. При этом восполнение расходной статьи бюджета логистики произойдет при улучшении уровня обслуживания клиентов и, как следствие, повышении объемов продаж компании (интенсивный рост продаж может составить 25%).
Рассказывает практик
Валерий Анохин, Начальник отдела логистики компании «Декёнинк Рус», Москва
Мы выявили несколько проблем, которые мешали оперативной работе. Расскажу подробнее о наших методах оптимизации склада.
Пересортица. На нашем складе вместе хранилось множество артикулов, из-за чего время от времени при отгрузке продукции заказчику возникала путаница. Это влекло и недовольство клиентов, у которых из-за несвоевременных поставок нарушался производственный процесс, и неточности в отчетности по остаткам. Мы ввели систему адресного хранения, адаптированную к нашему программному обеспечению. На подготовку и внедрение ушло около двух недель. Как только человеческий фактор был сведен к минимуму, проблема была решена.
Частые поломки техники. Высокие темпы амортизации машин влекли за собой регулярные поломки, частые срывы процесса отгрузки-погрузки, нарушение функционирования склада (вплоть до полной остановки работ). Подрядчик, обслуживавший технику, решал вопрос в течение трех дней или даже дольше. Справились мы с этой проблемой просто: заменили старого подрядчика на нового, который базируется ближе к складу. Теперь такая достаточно частая поломка, как разрыв гидромагистрали, ликвидируется у нас в течение полутора часов (раньше на ее устранение уходило несколько дней).
Низкая эффективность складской системы. Это довольно распространенная проблема многих складов. Мы решили ее технологически, переняв опыт коллег из нашего бельгийского подразделения и установив выдвижные платформы с палетами. Смена оборудования увеличила полезную площадь склада в 10 раз. Вложения в новую систему хранения окупились за два с половиной месяца.
Говорит Генеральный Директор
Леонид Шляпников, Генеральный Директор компании «Совтрансавтоэкспедиция», Москва
Наш складской комплекс состоит из нескольких зданий с разными системами хранения: напольной, стеллажной, мезонинной. Сейчас мы реорганизуем работу с разными грузами – продуктами питания, автомобильными компонентами и запасными частями для машиностроительных производств, а также запускаем терминал с новым оборудованием для обработки международных и внутренних экспресс-грузов (посылок и сборных партий).
Программа изменений рассчитана на два года и нацелена на повышение интенсивности и эффективности работы складского терминала за счет качественных изменений в ней. Начав реализовывать программу, мы уже за первый год сумели увеличить выручку от складских операций более чем на 30%. Опишу несколько ключевых проблем на складе, которые мы планируем решить или уже решили с помощью этой программы.
Перегруженность зоны быстрой обработки. Чтобы повысить пропускную способность складского терминала, мы разделили зону хранения на секции в соответствии с оборачиваемостью разных товарных групп. Например, для бесперебойной доставки продуктов питания в сетевые супермаркеты на двух отдельных складах была организована полная цепочка по приему, обработке, упаковке, хранению и доставке сборных партий продуктов. Подобные меры в разных блоках позволили разгрузить зону быстрой обработки – освободилось около 40% напольной площади.
Недостаточно высокая скорость отгрузки. Мы выделили специальные зоны для обработки грузов по их типу, графикам обработки и комбинациям клиентов. В каждой установлено специализированное оборудование для сбора заказов, наклеивания ярлыков и упаковки. Например, у клиента с большим количеством мелких партий, хранящихся в лотках на мезонине, зона для сборки и погрузки прилегает непосредственно к мезонину, что делает процесс сбора заказов и их отправки более удобным и быстрым. Благодаря этому скорость отгрузки увеличилась примерно на 15–20%.
Невысокая производительность центра обработки заказов . Раньше каждый оператор отвечал за работу только с одним, максимум с двумя клиентами. Мы организовали единую диспетчерскую службу, определили клиентские группы, которые объединили по номенклатуре, типу операций и графикам обработки. Таким образом выросла производительность каждого оператора – теперь он может отвечать за работу с тремя-пятью клиентами.
Недостаточно гибкая и эффективная организационная структура. Чтобы решить эту проблему, мы реформировали организационную структуру – теперь она привязана к отдельным клиентским проектам и их комбинациям. При этом мы стремились сохранить весь персонал. Начали с введения учета рабочего времени и поставили часть зарплаты в зависимость от показателя выполнения разных складских операций. Те из них, что требуют повышенного внимания сотрудников склада или специальной профессиональной подготовки, выполняются только допущенными к ним категориями работников и оплачиваются по более высокой ставке. Это позволило повысить не только эффективность, но и качество работы склада.